Dispelling the Myths about Manufactured Housing
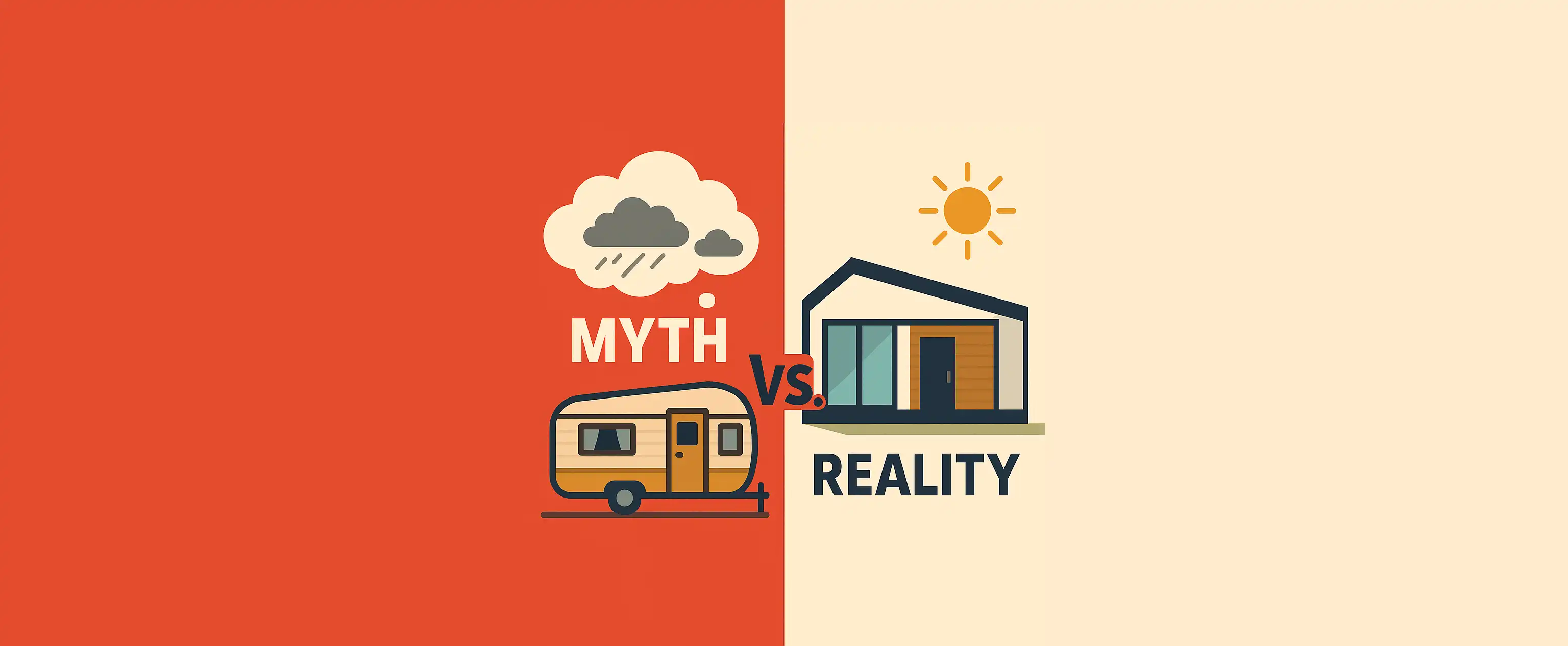
Manufactured, Modular, Tiny Homes and Prefab: Are they the same, different, or does it even matter?
In the world of homebuilding, terms like manufactured, modular, and prefab get thrown around a lot—and often interchangeably. While these types of housing are generally all built using a factory for either part or the majority of the construction process, there are key distinctions that matter – and some that really don’t.
Given this is a rapidly-changing and fast-emerging side of the construction sector, there is a lot of MIS-information out there on the internet, and we will try here to set the record straight for the moment - by providing facts and key regulatory references.
Whether you're a potential homebuyer, a developer, or just curious, understanding how to decipher facts from fiction is essential to making the right decision for your project.
What Is Prefab Housing?
Let’s start with the broadest category: prefabricated housing, or prefab. This is an umbrella term for any home that is partially or wholly built in a factory before being transported to its final location.
Manufactured homes, modular homes AND Tiny Homes are all types of prefab housing—but not all prefab homes fall into these categories. For example, panelized homes (where walls and roof sections are shipped separately and assembled on-site) or tiny homes on wheels could also be considered prefab.
In short:
- Prefab = any home built off-site and assembled on-site.
Note that the way prefab housing is permitted when panelized like a kit of parts is different from how other forms of prefab are permitted, and this can significantly impact the actual process and speed with which it can be installed. Be sure to do your due diligence on a company and its process if you are thinking about building a home or multifamily housing using a form of panelization, because the regulatory process may be less straightforward than choosing either traditional construction or what we call “volumetric” prefab, wherein the home is sealed up in a factory sufficiently to be inspected and approved while still at the factory.
Now let’s look at the two names most often used for volumetric prefab housing: Manufactured & Modular Homes.
The Myth of Manufactured vs. Modular Homes
Manufactured homes and Modular Homes are both a type of prefabrication that builds homes entirely in a factory and transports them to the site in one or more sections.
Cassette uses these terms interchangeably - because in ours and many others’ cases, the product is 100% interchangeable. The difference in industry terms and where they came from is a regulatory one, not a technical one. Specifically, the regulatory process whereby they are permitted, inspected, and approved by the regulatory authorities.
When most people refer to Manufactured Homes in the U.S., they refer to homes that have been built to a federal building code called the HUD code, a standard that regulates design, energy efficiency, quality, transportability, and safety of the home. HUD codes have specific structural and energy calculations that apply differently to different regions of the country, much like your local building codes address the specific safety dynamics of your region.
Other Key HUD characteristics:
- Built on a permanent steel chassis for safe transport.
- Are allowed to either be placed on temporary or permanent foundations.
- Have the unique option of remaining as personal property unless permanently affixed to land, which requires them to be legally converted to real property.
The predecessor to modern Manufactured Housing was the mobile home - but when the HUD code was introduced, upgrading the requirements and building standards of these homes in 1976, they evolved into a wide range of what are now classified as Manufactured Housing and referred to as either Manufactured or Modular Housing.
Modular homes are typically referred to as such because the client is going to install them on a permanent foundation and make them real property. Note that a modular home can come from a HUD-regulated factory, but can also come from factories building to local building codes under regional programs. In California, the department of Housing and Community Development (HCD) oversees permitting and inspection activities for homes built both to the HUD standard and to California Standards, which in many cases are identical.
Non-HUD Modular homes must specifically meet local, state, or regional building codes—the same as traditional site-built homes.
Other Key characteristics of non-HUD Modular Homes:
- Built in whole or in sections (modules) in a factory.
- Always assembled on-site on a permanent foundation.
- Classified at the outset as real property.
So What is a Tiny Home?
A Tiny Home is a type of manufactured home which, like it sounds, is quite small…it is required to be <400sf, AND it is built on a chassis. Again, the building code is what distinguishes a Tiny Home from either a Manufactured or Modular home — because it is only required to be built to what is called the ANSI code. This is a code that governs vehicles, rather than buildings, and so without any secondary designation, Tiny Homes typically can never become real estate – they remain mobile, personal property like an RV.
Key characteristics of Tiny Homes:
- Usually under 400 sq. ft.
- Often built on wheels for portability.
- Custom or DIY-built, using conventional building materials.
- May fall under RV codes (ANSI for park homes), IRC for permanent foundations, or not be certified at all, depending on local laws.
Summary:
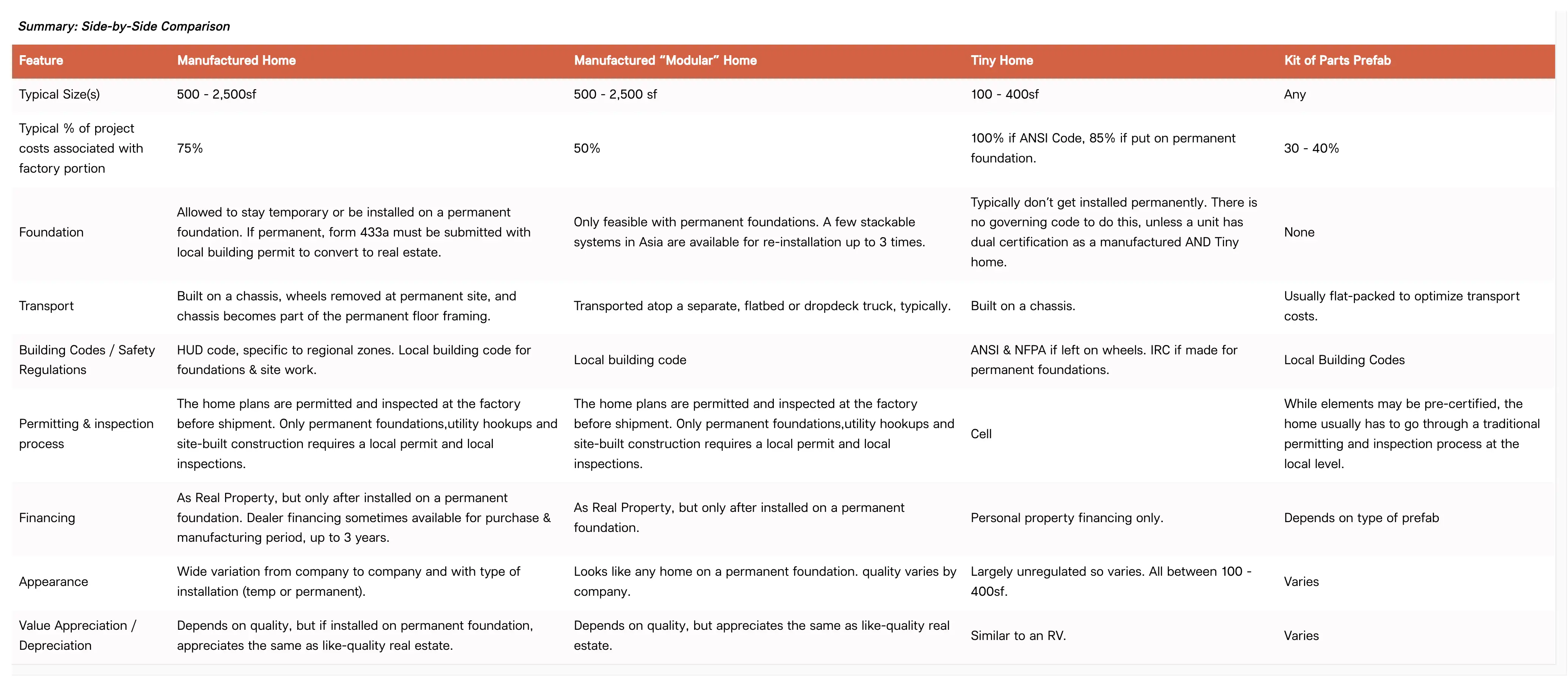
Does It Matter?
The prefab housing market is a broad spectrum. Cassette dove into this world in 2020 because we saw a specific use case for manufacturing in a “volumetric” way, which was to reduce the percentage of time and cost associated with the on-site components of building. We use Manufactured and Modular interchangeably, and have built our same homes using both HUD and Local certifications, depending on the factory agreements.
What matters is understanding what you, as a consumer or property developer, want to achieve with your project. As with anything else, it is important to use the right tool for the right job!
Final Thoughts
The prefab housing market is evolving rapidly, offering innovative and affordable alternatives to traditional site-built homes. If you are still confused - give us a call! We’d love to de-mystify the experience and help you find your way into a fabulous new home.
Whether you’re considering a manufactured home for cost-efficiency or a modular home for quicker construction and high-quality design, knowing what you're getting—and what it’s called—can make a big difference in your journey to homeownership.
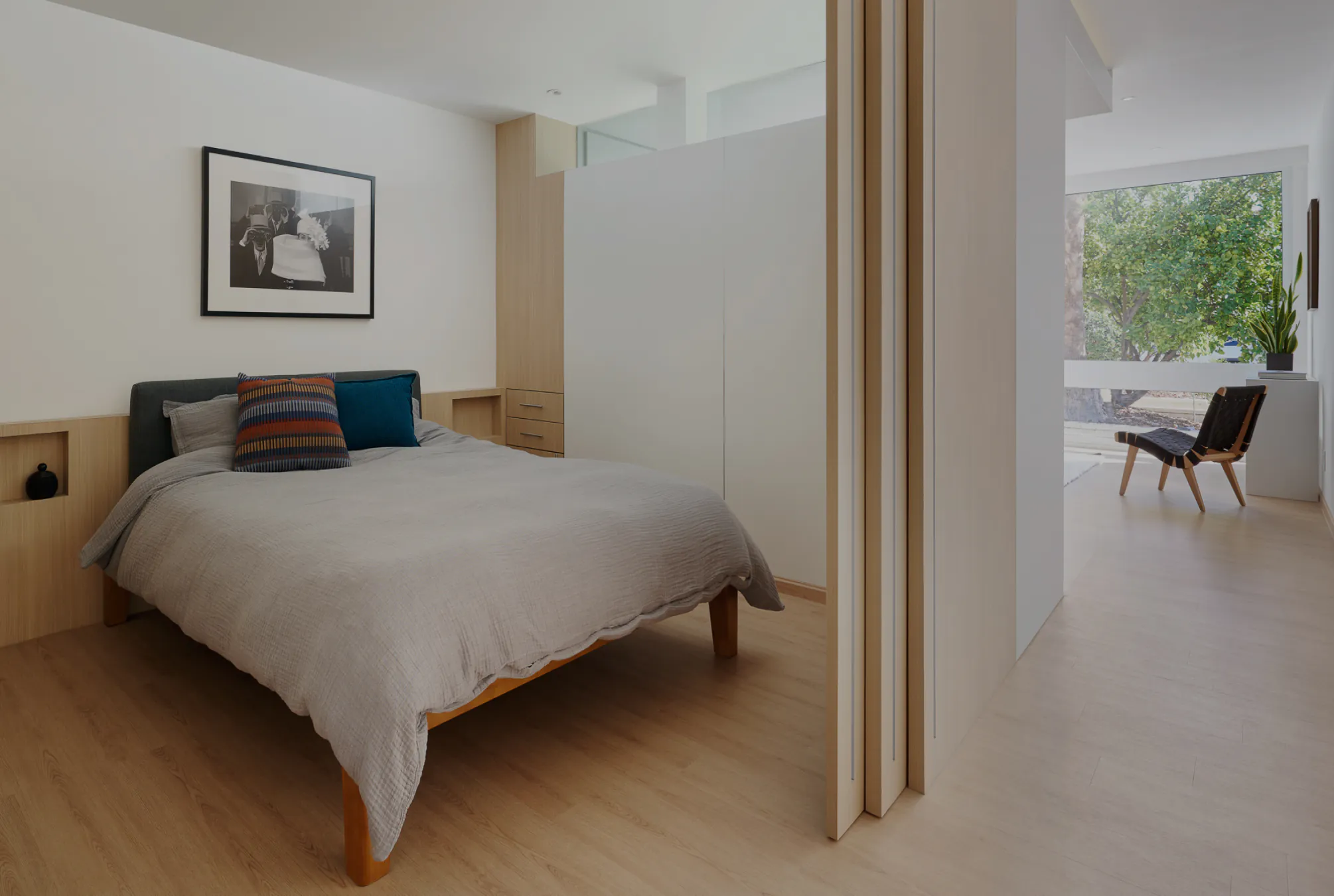